Reshoring: The return of American manufacturing
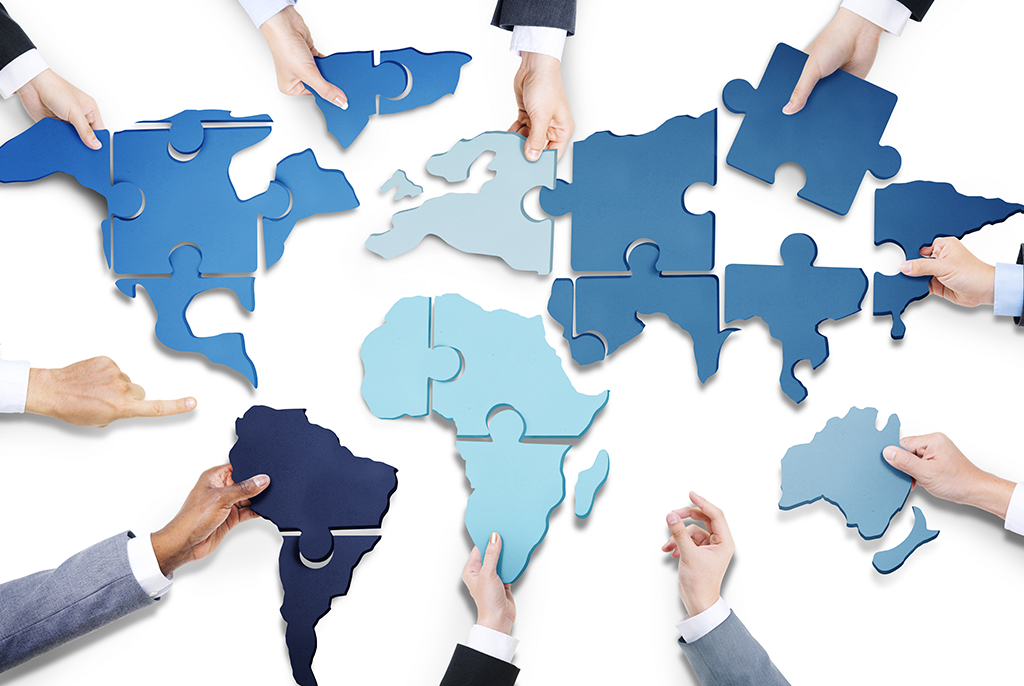
The offshoring of American manufacturing has sparked rancorous debate. Rooted in history, including the Industrial Revolution and our superiority in World War II, American manufacturing was a source of universal pride. The offshoring of American jobs to China and Korea was hard to reconcile.
Automation — doing more with less
While it may be an inconvenient truth, automation through smart robotics and the like creates an output of eight to ten times that of manual workers.[i] The labor equivalent of manufacturing robots is about $2 per hour.[ii] With improved productivity, manufacturers can do more with less.
That said, automation is a confusing concept to many because it implies a one-to-one replacement of workers. In fact, most factories are really semi-automated and promote higher-paying jobs (albeit fewer of them). The skills required of a machinist today are closer to a computer programmer who is capable of configuring a machine to run through the night, thus multiplying his or her output.
While the loss of jobs may be troubling on its face, the advent of automation offers a tremendous opportunity for manufacturers, their employees and our economy. The advantage for U.S.-based companies bringing their factories back to America is the ability to improve service levels by running just-in-time and saving time on setup and tooling. Often, the cost savings provided offshore are offset by high inventory and carrying costs. The cost advantage in China is tempered by escalating wage rates. Further, American companies have come to accept that their intellectual property and operating processes are at risk.
There is an effort on the part of many U.S. manufacturers to “nearshore” in Mexico and South America. The U.S. manufacturing base is moving away from heavy manufacturing, such as automobiles, to more agile technologies. For example, the shift toward ecommerce and mass-customized products will offer new opportunities for providers to meet the changing needs of consumers, who are expecting to buy products shipped to their door the following day. Growth in manufacturing jobs in the last year included increases in sectors such as machinery (+8.8%) and confectionary (+5.8%) and away from high-labor industries such as cut and sew apparel (-9.9%).
Parallel tracks
I believe parallel tracks are required to ensure the resurgence of American manufacturing:[iii]
- U.S-based companies will have to take a stand. I do not offer this as some form of protectionism ideology, but more in the spirit of competitive advantage. The assumption has been that companies need to vastly reduce their costs to compete, but when considering the total cost of ownership, many are re-evaluating that position. They are finding that making products half a world away also brings complexity, risk and longer cycle times. While every company is different, for some, “Made in the USA” is a powerful marketing message. Some customers will demand that points of distribution be in close proximity to them. Some companies may make the strategic decision to shape their offer on value added instead of price.
Some considerations:
- Calculate your total cost. Companies often think about gross margin calculations but fail to fully recognize indirect and overhead cost burdens.
- Consider tax implications. Tax reform may impact numerous decisions including the depreciation of assets.
- Maximize government incentives that may offset your costs. The U.S Economic Development Administration as well as state and local incentives continue to provide opportunities for entrepreneurs to recoup their investments faster.
- Calculate transportation costs. Include the true costs to administrator supply chain and vendors.
- Consider long-term agreements with customers. If customers want just-in-time, they should also be willing to take on obligations to work with you for some time. If they are not, you should question their true commitment as a party worthy of such risk.
- Private companies need to influence government at the federal, state and local levels. Within our economy, there is complacency regarding the need to elevate the skills of American workers. The headlines focus on the unemployment rate (around 4%).[iv] All one needs to do is take a drive through the American heartland, in the small towns of Oklahoma or Pennsylvania, to see that our country faces massive underemployment. Seeing our workforce scrounge together a living as rideshare drivers is a national disgrace.
It’s time for an effort to retool workers so they can successfully reenter the workforce with new skills that support the use of computer-controlled machine tools, 3D technologies and the like. We need to advocate with our local economic development organizations, community colleges, state agencies and trade representatives to ensure that government programs promote opportunity for all.
It is exciting to see American companies investing in manufacturing. Let’s bring government along for the ride.
[i] The Kiplinger Letter: November 17, 2017
[ii] The Industries of the Future by Alec Ross
[iii] Reshoring Initiative by Weisfuse and Comerford, IndustryWeek
[iv] The Kiplinger Letter: November 17, 2017
Category: Business Operations
Tags: automation, Innovation, manufacturing